Table Of Content

Clear communication and adherence to the agreed-upon terms and conditions contribute to the efficient and satisfactory completion of the welding project. Executing welds successfully requires careful attention to several factors. Inspection protocols and compliance with customer specifications and industry standards are essential. Suitable material selection is crucial to prevent premature failure, and coatings and joining methods should be evaluated. If the weld does not provide sufficient strength, then either additional weld is needed, or the configuration of the welds may be changed to get acceptable results.
OF FABRICATION
SMAW can be performed in various positions, including vertical and overhead, making it suitable for welding in challenging environments. However, it has a lower deposition rate compared to other techniques, and the slag must be removed after each weld pass. The next article (Part 2) will discuss the topic of fillet weld design before moving on to butt joints. Designers use CAD software for finite element analysis (FEA) of weld designs. The three most important basic principles in weld design are strength, resistance to fatigue, and distortion.
Design For Manufacturing
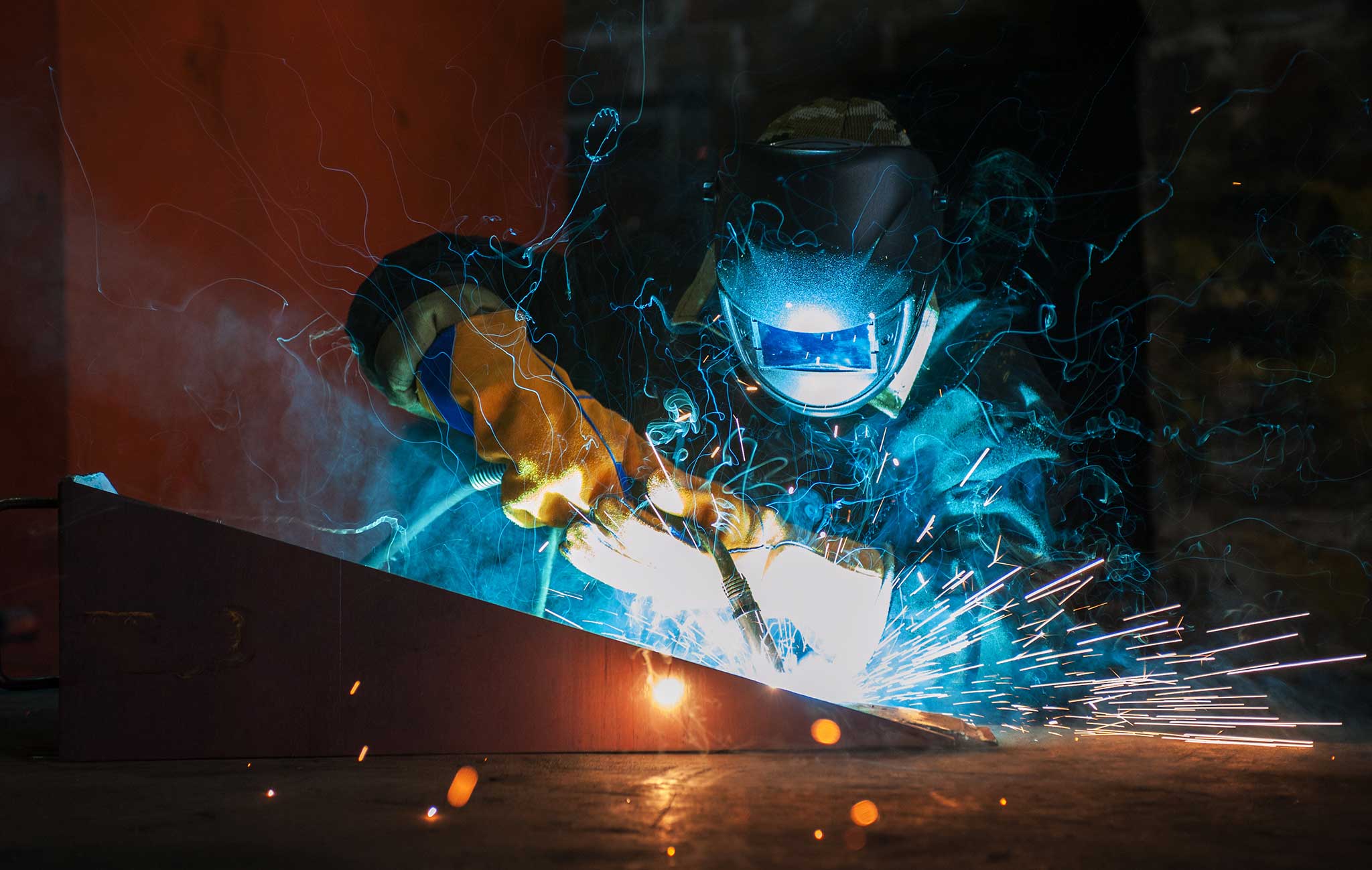
The first welding design code, known as the AWS D1.1, was developed in 1928 by the American Welding Society (AWS) to provide guidelines for structural welding.4. Weld design involves carefully considering factors such as the type of metal being used, the thickness of the material, and the desired strength of the weld.5. One of the challenges in weld design is the potential for distortion during the welding process, which can be minimized by using proper techniques and pre-planning the sequence of welds. Burn-through occurs when the weld penetrates too deeply, resulting in a hole or opening in the base metal. It can be caused by excessive heat input, improper joint preparation, or incorrect welding technique. To prevent burn-through, it is important to carefully control heat input, use proper joint design and fit-up, and employ techniques such as pulse welding or reducing travel speed.
How to Know if My Welding Machine Is AC or DC: A Comprehensive Guide for Welders
There are certain slot shapes which can promise more accuracy, but at the cost of strength. We feature in our store some of our best software to design, collaborate and innovate throughout the entire product lifecycle.
Design and fabrication of fine furniture is a challenging proposition. We bring our wealth experience with form and finishes to the table to help you through the process. Each step is just as important as the next, and we've got them all under control. Our Engineers are ready to work with you on your manufacturing equipment design needs.
Why is weld design important in manufacturing and construction?
Each classification has specific requirements and considerations, such as the materials being joined, the type of joint required, and the desired strength of the weld. Weld classification enables welders and engineers to select the most suitable method based on factors such as joint design, materials compatibility, and desired outcome. Successful weld design also requires considering fabrication processes and joining methods best suited for the project. Lack of fusion refers to a condition where the weld fails to bond with the base metal or adjacent weld passes. It can be caused by factors such as improper joint design, insufficient heat input, or incorrect welding technique.
What are the most common types of welds used in weld design?
Cobots Double Weld Grinding Efficiency Without Replacing Human Know-How - Machine Design
Cobots Double Weld Grinding Efficiency Without Replacing Human Know-How.
Posted: Thu, 16 Nov 2023 08:00:00 GMT [source]
Stress created for the three plate splice configuration weld equals plate thickness. Axial Normal Load Partial Penetration Weld thickness stress equation and calculator. The design of eccentrically loaded weld groups is primarily a trial-and-error operation. For every combination of design variables considered an analysis using methods of BGSCM 5.2 must be performed to determine the internal forces on the weld group. The worst-case force per unit length is then compared to the weld capacity. To determine the center of resistance of a weld group we use principles of statics.
Owner of Viking Metal Craft
The gas creates a containment-free environment, which improves the welding process. Achieving a good weld comes down to combining the right voltage with the proper wire speed, and this requires practice. Fine-tune the settings on the welder by practicing on the same material you plan to work with. In addition to the technical aspects of weld design, adherence to regulations and meeting deadlines is vital for the successful completion of welding projects.

Welding Helmets 2024: Expert Picks & Reviews - Forestry Reviews - Forestry.com
Welding Helmets 2024: Expert Picks & Reviews - Forestry Reviews.
Posted: Thu, 28 Mar 2024 07:00:00 GMT [source]
When it comes to welding design, several principles emerge as crucial. Firstly, strength plays a fundamental role in ensuring the durability and reliability of welded structures. It involves selecting appropriate materials, determining the optimal welding technique, and executing it accurately to achieve the desired strength levels. Secondly, resistance to fatigue is essential to maintain the integrity of welds under repetitive or cyclic loading.
Achieving a strong and durable weld starts with proper joint preparation. This section will guide you through the essential steps involved in preparing the weld joint, including cleaning, edge preparation, and fit-up. By following best practices in joint preparation, you can enhance the quality and integrity of your welds.
If the weld metal's strength exceeds the base metal strength, then increasing the weld's size further will not increase the strength of the connection. The weld size for which the weld base metal strength equals the base metal strength is known and the LARGEST EFFECTIVE size. Rounding up to the nearest 16th of an inch results in the largest effective weld size.